Data-driven Health Monitoring and Fault Diagnosis of Industrial Machinery Systems
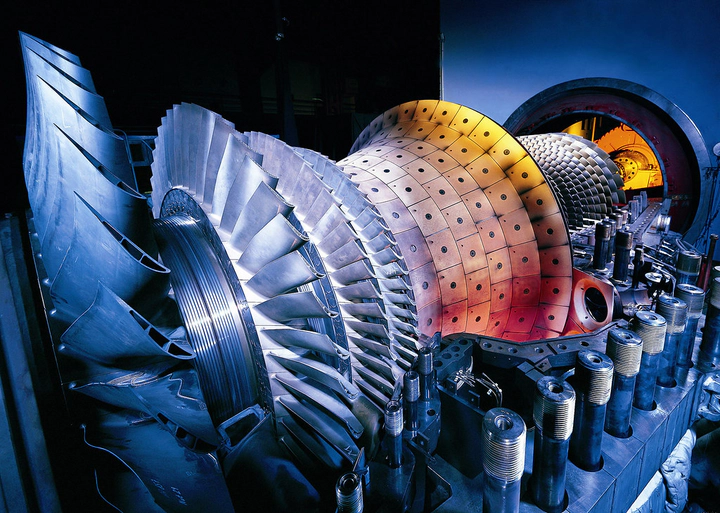
🙏Collaboration & Partners
This project is collaboration between University of Lincoln, Nanjing Agricultural University, Guangdong University of Petrochemical Technology.
Background
Industrial rotating machinery, such as gas turbines and multi-stage centrifugal air pumps, plays a critical role in various industries. However, unexpected failures can lead to operational downtime, increased maintenance costs, and potential safety hazards. Traditional fault diagnosis approaches rely heavily on scheduled maintenance and manual inspections, which may fail to detect incipient faults early enough.
With advancements in data-driven techniques and AI, there is a growing opportunity to leverage real-time condition monitoring and predictive analytics to enhance machine reliability and fault detection. This project focuses on developing an intelligent health monitoring system to proactively diagnose machinery faults and predict potential failures.
Objective
This project aims to design and deploy a data-driven condition monitoring system for industrial machinery to:
- Detect incipient faults early and prevent catastrophic failures.
- Apply advanced signal processing and machine learning models to analyze machine health states.
- Improve decision-making processes for industrial maintenance teams.
- Optimize predictive maintenance strategies, reducing unplanned downtime.
Key Features
- Condition Monitoring System Deployment – Installation of sensors and IoT-based solutions for real-time data collection.
- Fault Diagnosis using AI – Development of machine learning-based anomaly detection and classification models for fault identification.
- Data-Driven Insights – Analysis of vibration, acoustic, and temperature data to assess machine health.
- Predictive Maintenance Planning – Integration of early warning systems to trigger maintenance before severe damage occurs.
- Decision-Support System – Implementation of automated alerts and visual dashboards for engineers and operators.
Impact
This project enhances industrial reliability, operational efficiency, and maintenance strategies by transitioning from traditional reactive maintenance to proactive, AI-driven diagnostics. By applying data-driven fault diagnosis and predictive modeling, industries can reduce maintenance costs, extend equipment lifespan, and ensure safer operations.
Future research will focus on real-time deployment, system scalability, and continuous learning AI models for enhanced fault prediction accuracy.
Featured Outputs
📓- Zhiqiang Huo, Miguel Martínez-García, Yu Zhang, Lei Shu.
“A Multi-sensor Information Fusion Method for High-Reliability Fault Diagnosis of Rotating Machinery.”
IEEE Transactions on Instrumentation and Measurement (5-year IF: 5.6), 2021.
📓- Zhiqiang Huo, Miguel Martínez-García, Yu Zhang, Ruqiang Yan, Lei Shu.
“Entropy Measures in Machine Fault Diagnosis: Insights and Applications.”
IEEE Transactions on Instrumentation and Measurement (5-year IF: 5.6), 69(6), 2607-2620, 2020.
📓- Zhiqiang Huo, Yu Zhang, Gbanaibolou Jombo, Lei Shu.
“Adaptive Multiscale Weighted Permutation Entropy for Rolling Bearing Fault Diagnosis.”
IEEE Access (5-year IF: 3.7), 8, 87529 – 87540, 2020.
📓- Zhiqiang Huo, Yu Zhang, Pierre Francq, Lei Shu, Jianfeng Huang.
“Incipient Fault Diagnosis of Roller Bearing using Optimized Wavelet Transform based Multi-speed Vibration Signatures.”
IEEE Access (5-year IF: 3.7), 5, 19442-19456, 2017.